Few housing promotions in Spain that have been made, totally or partially, in a factory. And it is estimated that its implementation is barely around 5%, although their growth prospects in the coming years are significant. “More and more promoters and builders are studying in their tenders to be able to incorporate industrialized components,” says Juan Antonio Gómez-Pintado, president of the building cluster and the Corporation Vía Agora. Proof of this is that in the country there are 10 industrialized bath factories and that some of the most important promoters have already premiered, such as the quoted Aedas Home, via agora or culmina.
Industrialized construction implies producing in a factory the modules, pieces and elements that are then assembled in the field, which has obvious advantages over traditional construction. “It allows saving execution time and costs associated with the construction process, in addition to a more rational use of materials, the use of natural resources and waste reduction,” says Marta Vall-Llossera, president of the Superior Council of the Colleges of the Colleges of Architects of Spain (CSCAE).
The reduction of deadlines is very relevant: up to 40%. In addition, this way of building saves. “The future of the sector without industrialization is not understood,” says Gómez-Pintado. The businessman recalls that 30% of the workforce is retired in the next 10 years and only 5% is being incorporated. Without ignoring the fact that different regulations force the use of more sustainable materials, such as wood. The sector has been insisting on the need to transform the business, which is still very handmade, into a true industry. And they warn that if you do not take the step it will be very complicated. “This path is the only one that will increase the ability to produce the homes that our society needs,” says José María Quirós, industrialization delegate of Aedas Homes. Although this does not mean, neither now nor later, that only housing in factories are going to be made. Vall-Llossera is resounding: “except in counted areas, it is impossible to part with the usual construction.” In addition, land movement, foundation and a good part of urbanization works are executed in a traditional way.
Given the urgency to build, especially affordable floors, the Government announced last January a new strategic project, housing belongings, aimed at promoting the innovation and modernization of the industrialized and modular construction sector, to be able to build houses in less time and reverse as soon as possible the serious crisis of access to the housing suffered by the country. Along these lines, the leader of the PP, Alberto Núñez Feijóo, praised a few days ago the prefabricated houses as a great solution. Some social media users criticized Sanchez’s announcement by mistakeing, mistakenly, factory work with poor quality. However, it turns out to be the opposite. “Promoting construction industrialization does not mean making worse houses, but applying technology and efficiency to build faster, better and with a lower environmental impact,” explains Gómez-Pintado. Faced with the delays and errors that are made in the work, it is committed to manufacturing processes “similar to those of the automobile or aeronautical industry.”
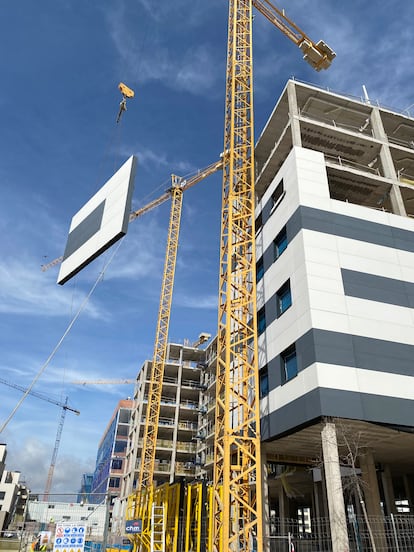
Ran from a facade of Lignum Tech in a promotion of Aedas Homes in Cañaveral (Madrid).
AEDAS HOMES
This achieves millimeter precision. Each home is subject to strict quality control. “These practices guarantee the final results and compliance with the standards, drastically reducing the final work work and almost completely eliminating the after -sales services with the reduction of costs that it entails,” says Quirós.
This does not imply, for the moment, that the final price of an industrialized floor is cheaper for the buyer, especially if structures and wooden envelopes are used, which have a 3%extra cost. “The trend of traditional construction costs will be to rise, and those of the industrialized one, to stay,” says Quirós. Because, in the end, time is money. “An improvement of execution times and a greater capacity for future adaptation should result in sales prices, taking advantage of the economies of scale,” adds the president of the CSCAE. “This is a future bet,” concludes Gómez-Pintado.
One of the pioneer promoters is Aedas Homes, which since 2018 has launched (delivered and in development) 6,730 homes totally or partially industrialized in 105 promotions. They total more than 12,000 industrialized baths. Some homes have been manufactured totally offsite (in factory) with 3D modular systems and others integrate prefabricated components such as structures, bathrooms, facades or stairs. The firm, which does not have its own factory, but works with the main bathroom manufacturers, concrete and wood structures, promised that From 2023 25% of the homes delivered were totally or partially industrialized. “Now we raise this commitment to 30% from 2026,” says Quirós.
The pioneers
The promoter via Agora, whose residentials have a high percentage of industrialization, is another of the leading companies. He develops two promotions in Navalcarnero (Madrid) with different industrialized systems, which will allow him to compare and draw conclusions. The business group to which it belongs, Corporation Vía Agora, began manufacturing industrialized bathrooms with Conspace in 2014 and in 2021 created Lignum Tech, specialized in developing facades and industrialized bathrooms. It has two factories in Cuenca and builds one more for the first transformation of the wood, having all the verticality of the
Industrialization walks, but faces important challenges, such as the need to develop an industrial fabric. “It is necessary to create an industry that can respond to the challenge and a professionalization in the trades, which, at the moment, is far from what is required,” says Vall-Llossera. But if there is a bottleneck is that of financing, since the traditional one does not work with an industrialized model. “I think a specific financing model for industrialization should be created. In this way, the expansion and creation of new factories would be promoted and the construction systems that are not installed on site could be financed, ”says the president of the building cluster. This association holds meetings with the European Investment Bank and the ICO, in addition to public administrations, to analyze what to do. It is also necessary to adapt different regulations, because it is not the same to build in situ as offsiteQuirós ends. According to Aedas Homes, the administration could prevail the use of industrialized construction in the bidding sheets of their works, helping to finance the new factories and even allowing to increase buildability in cases where modern construction methods reduce the trace of the footprint of Carbon generated by buildings.